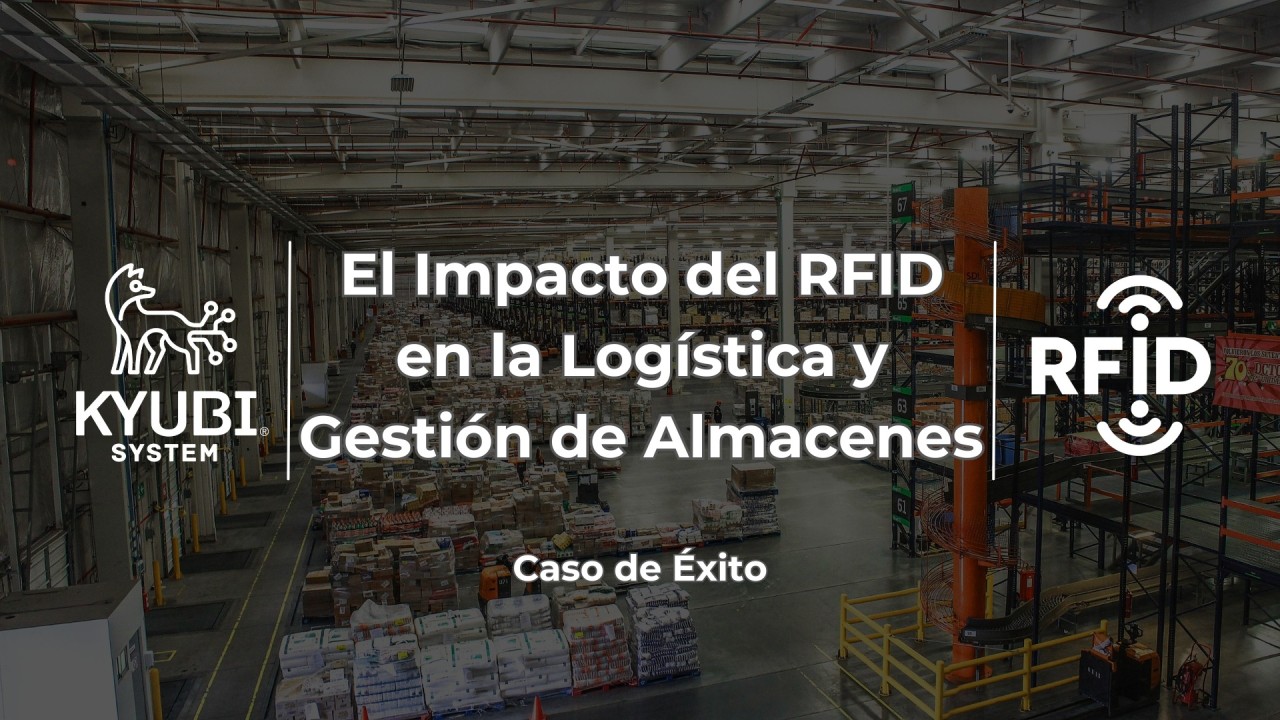
The RFID Logistics Revolution
In a world where logistics efficiency is key to competitiveness, RFID technology has become a fundamental element for companies seeking to optimise their warehouse management , reduce costs and improve product traceability.
With the increasing digitisation of the industry, RFID systems in logistics have replaced traditional manual processes, enabling greater accuracy, speed and control in inventory management. In this article, we will explore how this technology is transforming the industry and analyse a real-life case study that demonstrates its impact.
What is RFID and how does it improve warehouse management?
RFID (Radio Frequency Identification) technology enables the automatic identification and tracking of products through the use of electronic tags that store information and can be read without the need for physical contact.
Unlike barcodes, which require manual scanning and direct visual contact, RFID allows the simultaneous reading of multiple items in seconds, optimising efficiency in warehouses, distribution centres and the entire supply chain.
Key benefits of RFID in logistics:
-
Inventory control automation: reduced human error in counting and inventory speed.
-
Faster goods receipt and dispatch: Hundreds of products can be scanned in seconds and validated against system documents, ensuring reduced errors.
-
Reduced operating costs: Less labour time in counting and identification processes.
-
Real-time traceability: Precise location of each product within the warehouse and management of each movement.
-
Theft and loss prevention: Greater control over stock and goods in transit.
-
Optimisation of the supply chain: Improved management of logistics flows and delivery times.
Practical example: Without RFID, a 10,000-item warehouse could take up to 8 hours to do a manual inventory with barcodes. With RFID, the same process is done in less than 30 minutes with 99.9% accuracy.
Case Study: RFID Implementation in a Logistics Centre
Company: Global Distribution Company (Name withheld by NDA)
Sector: Logistics and distribution
Location: Europe
Objective: To optimise inventory management and reduce operating times in warehouses.
Problem before RFID implementation:
-
Inefficient manual processes: Inventory counting took more than 8 hours, leading to delays in the supply chain.
-
Errors in product identification: A 5% failure rate in recording and locating items.
-
Lack of stock visibility: Could not locate goods in real time, affecting delivery times.
RFID solution implemented:
-
RFID tags on each product and pallet for automatic identification.
-
RFID antennas strategically placed at entry and exit points of the warehouse.
-
Integration with warehouse management software (WMS) for real-time monitoring.
Results after 6 months of implementation:
-
Reduction of inventory time from 8 hours to only 30 minutes.
-
Traceability accuracy of 99.9%, eliminating errors in stock recording.
-
25% increase in operational efficiency in warehouse management.
-
18% reduction in operating costs related to stock management.
-
35% faster dispatches, improving end-customer satisfaction.
Conclusion: The implementation of RFID in logistics allowed this company to optimise its processes, reduce costs and increase operational efficiency, ensuring a better customer experience and a higher return on investment.
How to Implement an RFID System in your Warehouse
If you are considering integrating RFID technology into your business, it is important to follow a strategic approach to maximise the benefits:
1. Warehouse assessment and specific needs
Before implementing RFID, it is essential to analyse the warehouse structure, type of products and internal processes. It must be determined whether it is necessary to use active, passive or semi-passive RFID tags, depending on the level of traceability required.
2. Choosing the right hardware
An effective RFID system requires the following components:
-
RFID traceability software integrated with the WMS/ERP.
-
RFID tags (depending on the type of product and environment)
-
RFID readers for scanning goods in motion
-
RFID antennas in strategic areas such as loading docks and storage areas.
3. Integration with management software (ERP or WMS)
To maximise the benefits of RFID, the system must be integrated with ERP or WMS (Warehouse Management System) software to enable real-time inventory management.
4. System testing and optimisation
Before a large-scale implementation, it is advisable to conduct a pilot test in a specific area of the warehouse. This allows you to adjust settings, identify possible errors and optimise the system before expanding it completely.
5. Staff training
For a smooth transition, it is essential to train the logistics team in the use of the new RFID system. This will ensure that staff make the most of the tools available and minimise errors in the operation.
Why Choose Kyubi System for RFID Implementation?
-
Consultancy and advice tailored to the needs of your business.
-
Turnkey RFID systems, from the choice of hardware to the integration with your ERP.
-
Fast and scalable implementation, minimizing interruptions in your operation.
-
Technical support and training to ensure effective system adoption.
Request a free consultation and discover how RFID technology can transform your warehouse.
Contact us today: info@kyubisystem.com