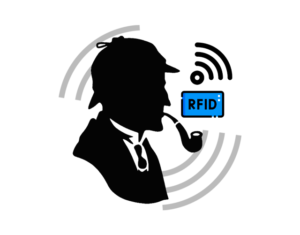
Warehouse management has been one of the most arduous tasks since teh beggining of times. Knowing what is there, where it is or when a product or raw material has been moved is a challenge; it also brings with it problems, errors and significant losses.
With rfid technology for inventories, the time has come to put an end to tasks that are more like the great Sherlock Holmes’ investigation than a warehouse management job.
In particular, RFID technology is the natural evolution of bar code scanning in logistics processes. It solves the traditional problems of manual warehouse control and management. In addition, it brings a number of decisive advantages, such as bulk reading of packages, rapid inventory of available stock and real-time recording of all goods movements.
But if you want to know more about why warehouse management systems are a great improvement and and an excellent option for inventory control, simplifying many tasks, keep reading this post.
But first… A bit of history.
The rfid system for inventory control in context
And, to do so, I’ll tell you my personal story…
Many years ago, at the beginning of the millennium, I “inherited” the management of a completely manual warehouse. It was a polyester fibre manufacturing company and the warehouse was about 25-30,000 m2 and could hold up to 4000 t in 250-300 kg bales. In each lane there were about 40-50 bales arranged at 3 different heights. Of course, these bales were perfectly labelled individually (double label, on the front and on the side) along with a serial number printed in a font of at least size 14 body size.
The perfect storm. More than 15,000 bales, 350 lanes to locate, paired less than 1m apart between pairs and labels printed with a 12-digit size 14 number. Stitching. Every day the location map had to be done and redone several times, mistakes were a constant and when a package was misplaced … even Sherlock Holmes couldn’t find it.
Sound familiar? An army of warehouse staff placing, pointing, relocating, re-pointing, manual packing lists, 2 and 3 manual checks before, during and after loading to check that what came out matched what was supposed to come out. Constant stock-outs, missing packages (or mis-shipped, we didn’t really know anymore), and everything depending on the operator’s skills and memory to minimise the incidences.
So we decided to end it. We opted for a barcode-based solution because the issue of RFID warehouse tags was at that time too expensive in comparison, as well as it was also somewhat embryonic and unproven, and we needed to solve all the immediate problems urgently.
Our life changed. Like so many other warehouse managers who at that time opted to take the leap and do away with manual management. Labels with standardised barcodes allowed us to store relevant information on production, batches, etc., code readers and repeater antennas to transmit almost online the information on incoming and outgoing pickings, and to control the locations. All this is integrated with the company’s management system.
Today it is the most common, but this system has its limitations. Mainly because of the fact that the packages have to be read individually and if you do not have a fully automated warehouse, it does not completely eliminate the problems: erroneous or partial readings, difficulties in reading the code due to label’s location (distance, angle), movements in almost real time (there is always a certain delay in the transmission of data), laborious inventories…
20 years ago it was a matter of choice between manual or barcode; today, technological development has made RFID technology for inventories affordable to take the next step from barcode to RFID tag, and solving the vast majority of these problems without undermining the existing advantages, such as integration with the management system.
The main benefits of warehouse management systems
Bulk reading of packages. It is no longer necessary to read the tags one at a time (which can also be done), but they can be read in groups by passing them through an arch or tunnel, which is particularly useful for checking dispatches and verifying them against loading orders automatically, simply and without errors.
Fixed antennas capable of covering the entire warehouse can also be used, which are capable of inventorying the available stock at a single pass, as they do not depend on the tags relative positioning, they do not need direct vision: they emit the signal and receive the response from the tags of each bundle at the same time.
Every movement is recorded in real time as needed, improving warehouse management and the ability to make relevant business decisions quickly. For example, offers or promotions based on desired turnover or available stock levels. This reduces the risk of stock-outs.
All of this leads to a significant reduction in operating costs, which, for example, some studies have estimated at around 30% in retail, as errors and management time are minimised, as well as the need for human intervention in the processes.
RFID warehouse management is the natural evolution from bar coding. Its impact is at least equal of what you experience when you switch from manual management to barcoding. And it is no longer a leap of faith or a huge investment, as it is a proven technology with an attractive ROI.
At Kyubi System we are specialists in designing and implementing RFID technological solutions for inventory control and we can show you in a personalised way how you can make your business logistics profitable. Ask us with no commitment and bet on rfid warehouses in your company.